On September 9-11th, Smithsonian Libraries hosted the workshop: “Using Pigment-toned Paper Pulp to Create Flawless Fills for Works of Art on Paper and Archival Material,” instructed by Margo McFarland-Rothschild, who has taught these techniques previously at the Campbell Center for Historic Preservation Studies and has her own conservation and consulting practice in the Chicago area. At Smithsonian Libraries’ Book Conservation Lab participants prepared and pigmented paper pulp to use in concert with wet suction casting techniques to directly fill losses in paper based artifacts.
Works on paper such as posters, drawings, or pages of a book can all be damaged in way that results in lost original material. For example, this damage can occur as holes contained within the page or as tears along its edges in which the corresponding pieces are lost from the main artifact. This type of damage is referred to as a “loss.”

A traditional way of repairing losses is for a conservator to find a best fit from existing samples of paper and then making necessary modifications, such as trimming and color toning, to make a matching inset for the loss. This inset is then secured to the area of loss by appropriate adhesives. Often a type of Japanese paper is employed for these repairs, as discussed in the Fix’s post from March 2013. Though Japanese papers of often used to create the inset, many conservators and conservation labs also have a collection of historic paper samples gathered over the course of many years.
This approach has its limitations. The chances of having a perfect paper sample to perfectly match the original is unlikely. Colorants used to tone the inset can be problematic. They can bleed into the original or react in ways that are unhelpful to the conservator. Furthermore, thorough preparation aside, executing a truly seamless repair requires very delicate hand work to truly match and camouflage the repair at the point where original and mend meet.
Using paper pulp to fill losses is advantageous alternative method because it is custom-made to the loss. The pulp itself can be mixed to very closely match the original paper structure of the item and, when directly cast into the area of loss, the pulp will bond with the original item without need for additional adhesives to secure the insert in place; a seamless connection. While wet, the pulp fill can be textured to mimic any markings on the original. And, critically, when the pulp is pigment-toned using the demonstrated process (more detail below) the toning will be permanent, eliminating any concerns about the colorant leaching into the original, either during treatment or any subsequent aqueous treatments. (For those of you who may find it hard to believe, washing paper, including very old and/or brittle paper, in water baths, completely submerging the paper under water, is a common conservation practice.) The custom pulp fill technique is also completely reversible.

The first step in the workshop was to prepare and pigment pulp that would later be used to fill losses. We used pulp of varying fiber compositions that was “ready to use” and that was then mixed with pigments in a simple kitchen blender. (The wet, ready-to-use pulp and the pigments were purchased from Twinrocker Hand Made Papers.)
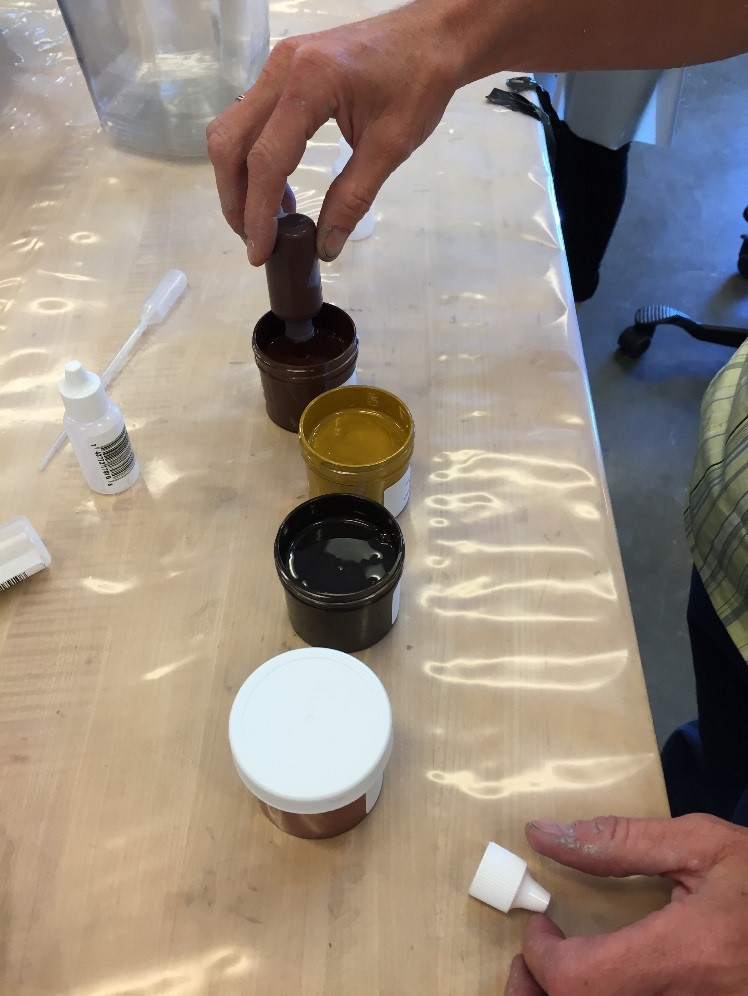
In the process of beating cellulose plant fiber into pulp an anionic charge (negative) is imparted to the pulp fibers. Further fibrillation of the fibers in our blenders also increased this charge. The pigment, used in combination with a retention agent, carries a “+” or cationic charge. Therefore when pulp and pigment combine they bond and the pigment dyes the pulp permanently. We experimented with different combinations of pulp, pigment colors, and retention agents.
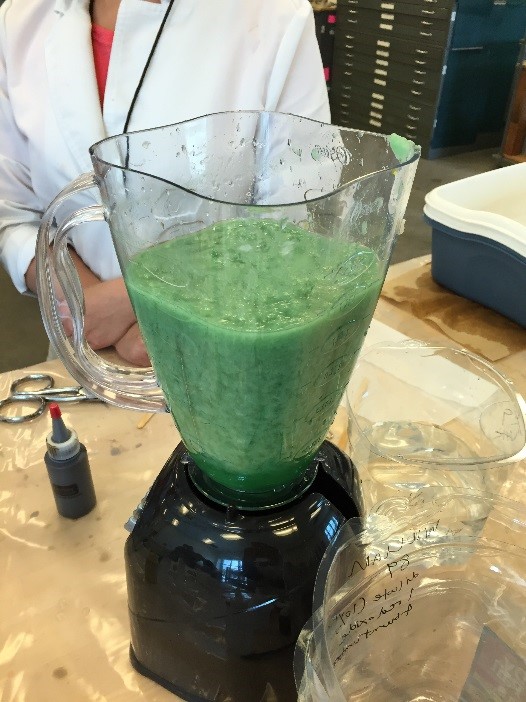

The next step was to cast the slurries to form sheets of paper which expressed their varying characteristics: type of fibers used, colorant(s) added and etc. We used Twinrocker’s paper making kit, “Dish Pan Mould,” to cast the sheets.


These cast sheets allowed us to see how the varying combinations of pulp and pigments created papers of not only different colors but textures and structure. These sheets can then be reconstituted back into pulp slurries for the direct casting of fills at a later time. We also discussed the potential for using the fine edges of the pulp castings with methyl cellulose as an adhesive to mask blemishes or to help camouflage paper repair mends.
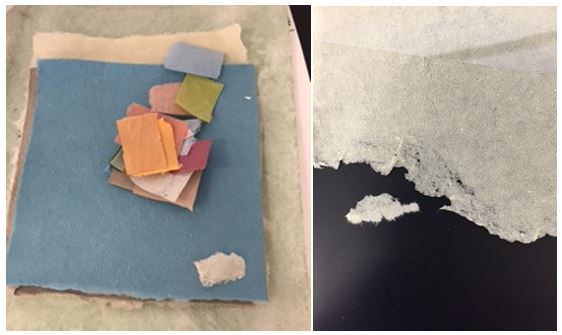
Once we had cast sheets of pigmented pulp and familiarized ourselves with process of preparing and pigmenting pulp slurries, we practiced wet suction techniques to cast the custom pulp fills. Different techniques and equipment set-ups were demonstrated and practiced with. To start, we used the Twinrocker moulds that were used for casting the pulp earlier in the workshop.

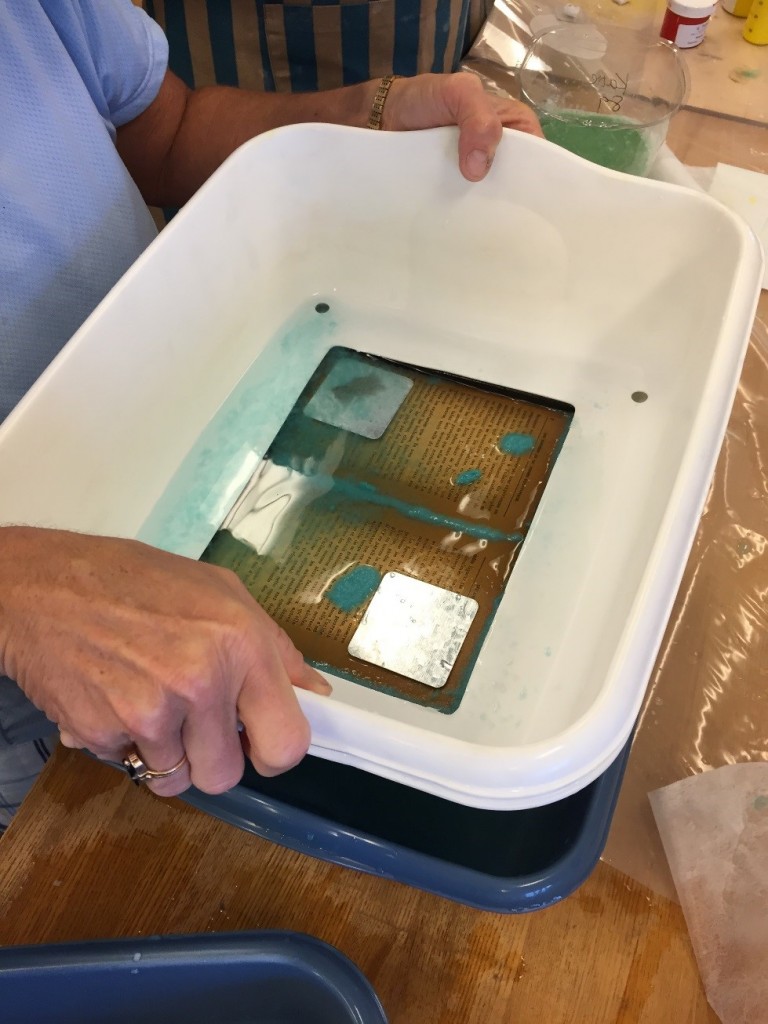

There is a balance to be found between the amount of pulp incorporated in the slurry and the speed with which the water/slurry is filtered, which creates a useful amount of suction to pull the pulp into the area of loss and determines a successful fill. This could be regulated by simply pulling the mould more or less quickly from the pan of slurry or by the material used as a screening filter. We practiced with different filter screens to control the pace of filtration and different techniques and materials for masking off the damaged areas (sometimes no masking was used at all). We also practiced different methods of couching and drying the filled area, and to help impart matching texture to the repair; pressing and sometimes even burnishing the custom pulp fill.

Another technique and set-up demonstrated was based from a silk screen frame that allowed for larger items to be treated and which used a suction table to control the slurry filtration speed.

We also experimented with a large tub and crate which mimicked the Twinrocker paper mould kit but on a larger scale.


On the opposite end of the scale spectrum, experiments were made at the end of the workshop with a custom Mylar box of small size, constructed by one of the participants, which allowed a custom pulp fill to be cast without submitting the artifact to full aqueous submersion.


Suggestive of the experiments with the Mylar box technique performed on the suction table, participants further discussed and shared ideas for how to further apply the techniques demonstrated during the workshop.
Thanks to all participants for their enthusiastic ideas and work. Thanks to Smithsonian Libraries for hosting and preparation. Thanks to Margo for introducing many new ideas and techniques.
4 Comments
Great article! Are there alternative methods to using leaf casting machines?
Thanks for your interest! This method of leaf casting was developed for and is traditionally used in conservation, however, alternative uses and methods of this procedure may be available outside the field. It could be interesting to explore . . . With that said, alternative methods for paper repair abound! A common technique is explored in our March 2013 post.
Nice and informative article. Thanks for sharing all the information with us. Learned a lot of new things.
I plan on trying this on comic books…